Marconi (Alluminio di qualità): “Superyacht e alluminio sostenibile, un’opportunità ancora poco sfruttata”
L’azienda genovese punta sulla riduzione dell’impatto ambientale con energia green e nuove tecnologie di taglio. Il suo a.d. invita la filiera a educare il mercato sulle soluzioni già oggi disponibili
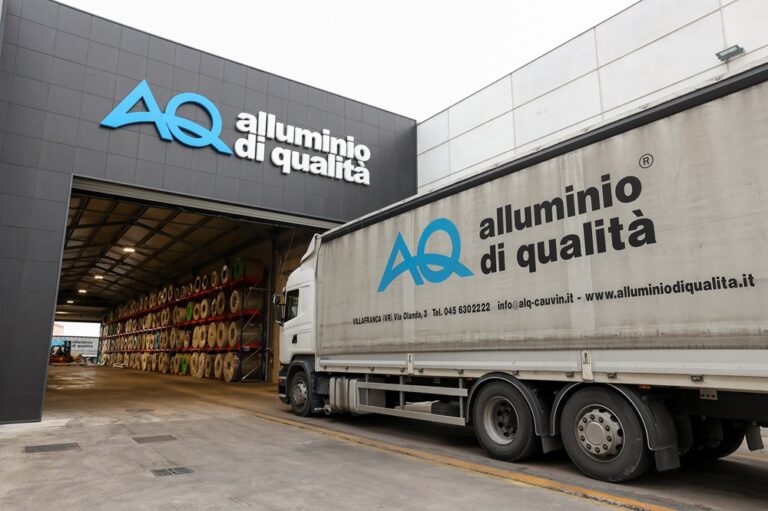
Fondata a Genova nel 1986, Alluminio di qualità è una delle aziende leader nella distribuzione e lavorazione di laminati piani ed estrusi in leghe di alluminio destinati a diversi settori industriali, dall’edilizia all’automotive fino alla cantieristica navale. Nell’ambito della tavola rotonda ‘L’alluminio e l’eccellenza italiana: innovazione, design e sostenibilità nelle costruzioni navali’ organizzata dalla rivista Alluminio e Leghe e moderata da Eugenio Paroletti in occasione della fiera dedicata alla filiera dell’alluminio Metef di Bologna, dopo Federico Rossi di Rossinavi ha parlato Mattia Marconi, a.d. di Alluminio di qualità, con un intervento sui risultati ottenuti riguardo alla sostenibilità del materiale e, allo stesso tempo, della scarsa consapevolezza di alcuni settori industriali al riguardo.
“Dai produttori dei semilavorati ai centri servizi, dagli operatori a valle fino ai clienti e ai consumatori finali si parla poco di sostenibilità. L’Italia eccelle nella filiera dei superyacht e battelli da lavoro che vede un consumo importante e crescente di alluminio, ma sono settori, penso di poterlo affermare senza essere smentito, in cui non c’è ancora piena consapevolezza di cosa è già oggi possibile fornire in termini di sostenibilità del materiale. E la nostra filiera deve prendersi la responsabilità, a mio avviso, anche di fare educazione in tal senso. Mentre l’upstream si è mosso da tempo e molti produttori di alluminio primario hanno il loro brand green, man mano che il metallo si trasforma nei semilavorati e si scende lungo la catena del valore, il concetto di sostenibilità del materiale si disperde”.
Come spiega questa dinamica?
“Ritengo che siamo troppo concentrati sulle richieste del cliente: se il cliente non chiede, non viene reso edotto di cosa è già disponibile. Questa è la prima responsabilità di cui noi, in qualità di centro servizi, dobbiamo farci carico insieme ai produttori di alluminio. A parte il settore automotive, spinto con forza a intraprendere un percorso sostenibile in anticipo, vedo ancora poca richiesta di alluminio a basso impatto ambientale. La cantieristica navale è un segmento in cui non c’è ancora una richiesta del genere, eppure la filiera è pronta a fornire materiale sostenibile”.
Cosa ha fatto Alluminio di qualità in tal senso?
“Abbiamo scelto di proseguire un percorso di sviluppo accogliendo una sfida, benché non richiesta dal consumatore finale, di garantire comunque una filiera e una tracciabilità del prodotto che consenta, laddove necessario, di avere un impatto minore”.
Quali azioni avete intrapreso, in concreto?
“L’aspetto principale è stato cercare di rendere green l’energia che consumiamo. Abbiamo installato impianti fotovoltaici per garantire l’autoconsumo della produzione, che oggi copre fino al 50% delle nostre necessità. Inoltre abbiamo affrontato il tema del processo di trasformazione dell’alluminio, fino a oggi un’attività appannaggio di una tecnologia di taglio al plasma diventata obsoleta da un punto di vista dei risparmi energetici che invece consentono gli impianti di nuova generazione”.
Avete quindi aggiornato gli impianti di lavorazione?
“Sì, è stato necessario un passaggio a nuove tecnologie di taglio laser a fibra ad alta potenza, impianti che un tempo non consentivano di tagliare e trasformare nel range di spessori richiesti da questa industria. La cantieristica navale, nel segmento super e megayacht, spazia da spessori compresi da 3 a 50 mm nei quali rientra tutta la gamma di prodotti, con una concentrazione particolare negli spessori che vanno da 5 a 20 mm. Una gamma che non consentiva di essere lavorata con le macchine di vecchia generazione, i nuovi impianti consentono invece di affrontare questa sfida e di farlo con incredibili risultati in termini di risparmi energetici e produttività. Lo scorso anno abbiamo quindi dismesso le nostre linee di taglio al plasma orientando la produzione su nuove linee di taglio laser a fibra, consentendo risparmi energetici di oltre il 20%”.
Quali sono le differenze principali tra le due tecnologie?
Quali sono i rimedi possibili per rendere più consapevoli le altre industrie?
“La nostra industria si è orientata a offrire alluminio a basso impatto nonostante manchi ancora questa sensibilità, ma come dicevo prima è anche compito nostro, ovviamente insieme ai clienti, cercare di analizzare le possibilità e i benefici che questa filiera è già in grado già di offrire. La sostenibilità comprende anche un migliore riutilizzo degli scarti di produzione che finiscono direttamente in fonderia e questo grazie anche alla vicinanza strategica al produttore Fusina”.
ISCRIVITI ALLA NEWSLETTER GRATUITA DI SUPER YACHT 24
SUPER YACHT 24 È ANCHE SU WHATSAPP: BASTA CLICCARE QUI PER ISCRIVERSI AL CANALE ED ESSERE SEMPRE AGGIORNATI
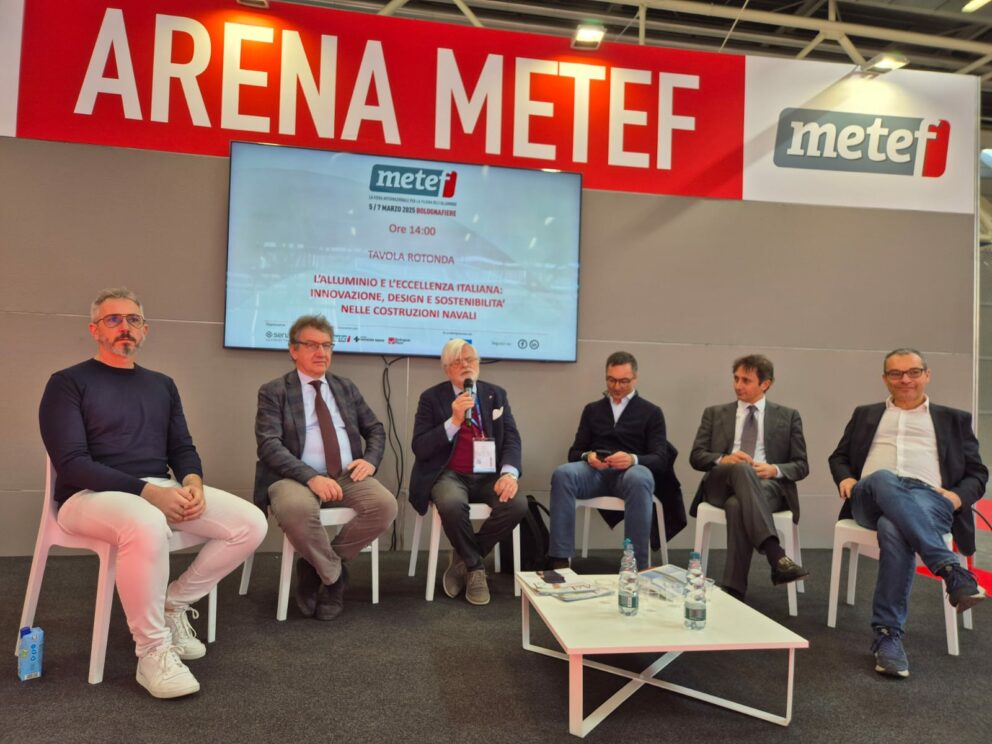
Da sinistra: Federico Rossi di Rossinavi, Franco Bonollo dell’Università di Padova, Eugenio Paroletti della rivista Alluminio e leghe, Vincenzo Zinni a.d. di Niche Fusina Rolled Products, Mattia Marconi, a.d. di Alluminio di Qualità e Guido Godani a.d di Metalluminio